Refractory Cement
Reliable Bonding • Superior Heat Resistance • Manufacturer Direct Supply
Refractory cement is a type of cement primarily composed of monocalcium aluminate or calcium aluminate as its main mineral component. It is produced by calcining or electrically fusing natural bauxite or industrial alumina with calcium carbonate (limestone) in a specific proportion. Some variants are also made by melting bauxite and limestone together. Calcium aluminate cement, aluminate cement, and high-alumina cement are collectively referred to as refractory cement. It is commonly used in the production of refractory concrete and castables, which can withstand extremely high temperatures, making it an indispensable raw material in industries such as steel, glass, and cement.
Characters of Refractory Cement:
•🔥High-Temperature Resistance: Sustains long-term temperatures of 1300°C–1600°C, with a maximum tolerance of up to 1800°C.
•🔄Thermal Shock Resistance: Withstands frequent cycles of heating and cooling without cracking.
•💪High Bonding Strength: Compressive strength at room temperature ≥40 MPa, with strength retention of over 70% at high temperatures.
•🛡️Chemical Corrosion Resistance: Resists acids, alkalis, molten salts, and metal melts.
•⚡Rapid Hardening: Initial setting time of 30–60 minutes, reducing construction time.
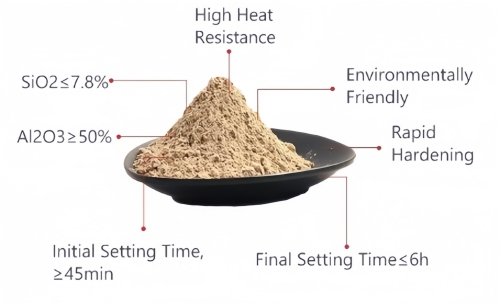
Typical Applications of Refractory Cement:
•🏭Industrial Kilns: Lining and repairing the interior of blast furnaces, rotary kilns, and electric furnaces.
•🔥Boilers and Hot Air Ducts: Sealing high-temperature pipe joints to prevent heat leakage.
•🛠️Metallurgical Casting: Lining of steel ladles and molten iron troughs to resist erosion from molten metal.
• �️ Fire Protection in Construction: Fireproof insulation layers for fireplaces and chimneys.
•⚠️Emergency Repairs: Rapidly repairing localized damage in high-temperature equipment (such as cracks and spalling).
Parameters of Refractory Cement:
Item | CA50-600 | CA50-700 | CA50-900 | CA70 | CA70W | CA70S | CA71 | CA80 | CA80S | ||
Chemical Composition | ω (SiO2) ≤/% | 7.8 | 7.5 | 5.5 | 0.5 | 0.5 | 0.5 | 0.5 | 0.5 | 0.5 | |
ω (Al2O3)/% | 50 | 51 | 53.5 | 68.5-70.5 | 68.5-70.5 | 68.5-70.5 | 69.5-71.5 | 78-81 | 78-81 | ||
ω (Fe2O3) ≤/% | 2.5 | 2.5 | 2.5 | 0.2 | 0.2 | 0.2 | 0.2 | 0.2 | 0.2 | ||
ω (CaO)/% | / | / | / | 28.5-30.5 | 28.5-30.5 | 28.5-30.5 | 27.5-29.5 | 17.5-20.5 | 17.5-20.5 | ||
ω (MgO) ≤/% | / | / | / | 0.4 | 0.4 | 0.4 | 0.4 | 0.4 | 0.4 | ||
ω (R2O) ≤/% | 0.4 | 0.4 | 0.4 | 0.4 | 0.4 | 0.4 | 0.4 | 0.4 | 0.4 | ||
ω (S) ≤/% | 0.1 | 0.1 | 0.1 | / | / | / | / | / | / | ||
ω (Cl) ≤/% | 0.1 | 0.1 | 0.1 | / | / | / | / | / | / | ||
Fineness | d50/μm | / | / | / | 4~11 | 8~11 | 6~9 | 10~13 | 5~8 | 5~8 | |
-45μm ≤/% | / | / | / | 8.0 | 5.0 | 5.0 | 8.0 | 5.0 | 5.0 | ||
Setting Time | Initial Setting Time (min) | ≥45 | ≥60 | ≥90 | 120-180 | 30-90 | 180-240 | 150-210 | 30-90 | 90-150 | |
Final Setting Time (min) | ≤360 | ≤360 | ≤360 | 150-240 | 90-180 | 240-330 | 210-300 | 90-180 | 270-360 | ||
Strength (ISO) | Flexural Strength/Mpa | 24h | 6.0 | 6.5 | 8.0 | 7.5-10.0 | 8.0-10.5 | 8.0-10.5 | 8.5-11.0 | 5.0-7.5 | 5.0-7.5 |
72h | 7 | 7.5 | 10 | 10.0-12.0 | 10.5-12.5 | 10.5-12.5 | 11.0-12.5 | 6.0-8.5 | 6.0-8.5 | ||
Compressive Strength/Mpa | 24h | 45 | 55 | 72 | 40-50 | 45-55 | 45-55 | 50-60 | 30-40 | 30-40 | |
72h | 55 | 65 | 82 | 45-55 | 50-60 | 50-60 | 55-65 | 40-50 | 40-50 | ||
325M ≤/% | 15 | 12 | 8 | / | / | / | / | / | / | ||
Specific Surface Areas ≥/ (㎡/kg) | 300 | 320 | 350 | / | / | / | / | / | / |
FAQ:
Q:What is refractory cement used for?
A:Refractory cement is used to line, bond, or repair high-temperature structures such as kilns, furnaces, boilers, fireplaces, and incinerators. It can withstand extreme heat and thermal shock without cracking.
Q:What is the maximum temperature refractory cement can handle?
A:Depending on the grade, refractory cement can withstand temperatures ranging from 1300°C to over 1700°C.
•CA-50: up to 1450°C
•CA-70: up to 1600°C
•CA-80: over 1700°C
Q:What’s the difference between high alumina cement and ordinary cement?
A: High alumina refractory cement contains a much higher percentage of Al₂O₃, giving it better heat resistance, faster setting time, and stronger performance at high temperatures compared to ordinary Portland cement.
Q:How do I mix and apply refractory cement?
A:Mix with clean water in a ratio of 2:1 to 3:1 (cement to water by weight) until a uniform paste is formed. Apply manually or via casting/vibration. For large projects, consult our installation guide or request our technical video support.
Q:Do you provide technical support for curing and drying?
A:Yes. We provide a furnace drying curve, step-by-step curing instructions, and even on-site guidance if needed. Proper curing is essential to ensure maximum strength and longevity.
Q:Can your refractory cement be used in steel plants and cement kilns?
A: Absolutely. Our CA-70 and CA-80 grades are widely used in steel ladles, rotary kilns, preheater towers, and burner zones. We can also tailor formulations for specific industry needs.
Q: What packaging options are available?
A:• 25kg moisture-proof kraft bags
• 1000kg jumbo bags for bulk shipments
• Customized pallets and OEM labels available upon request
Q:Do you offer OEM/Private Label services?
A:Yes, we support OEM services, including customized packaging, printed labels, and documentation to match your brand. Ideal for distributors and long-term partners.
Q: What’s your production lead time?
A: Typically 7–15 days depending on order volume and packaging requirements. We also support urgent orders with priority scheduling.
Q: Which countries do you export to?
A: We currently export to over 30 countries including the USA, Germany, South Korea, Saudi Arabia, UAE, Egypt, South Africa, and Chile. All products comply with international quality standards.
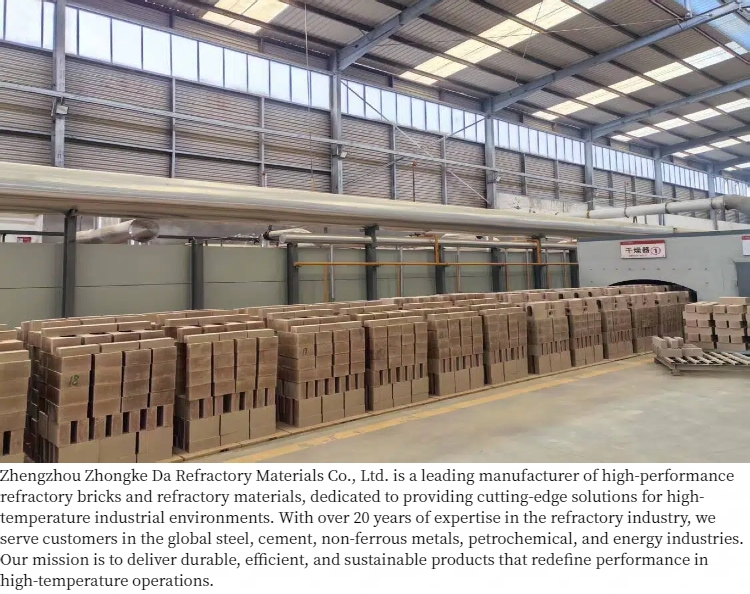

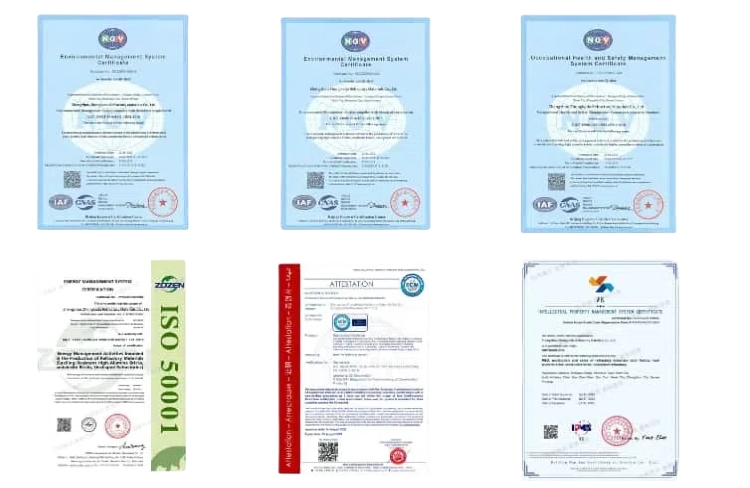
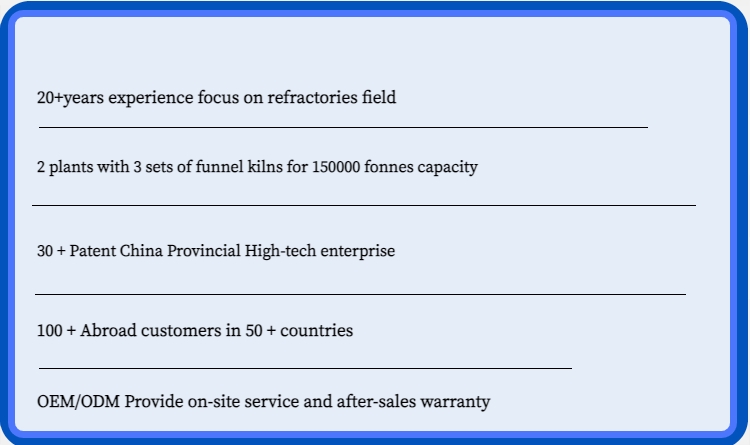